Improve processing with heat exchangers
Starch drying
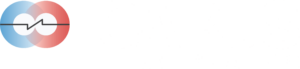
Elevating global standards with exceptional, unmatched Dutch craftsmanship in advanced industrial heat exchange.

Understanding Starch Drying: The Essentials
Starch drying is a pivotal industrial process that significantly enhances the shelf life and usability of starch extracted from various raw materials like corn, cassava, and potatoes. This process involves reducing the moisture content of wet starch to create a dry powder, suitable for a wide range of applications in food production, paper manufacturing, and the textile industry. The key to effective starch drying lies in the precise control of temperature and moisture levels, ensuring that the physical and chemical properties of the starch are maintained without degradation. This not only preserves the functional attributes of the starch but also optimizes its storage and handling characteristics. Through advanced drying technologies such as flash dryers and fluidized bed dryers, starch drying achieves efficiency and quality, meeting the stringent demands of modern industrial practices.

Exploring the Dynamics of Advanced Starch Drying Techniques
Starch drying is not merely a routine procedure but a sophisticated balance of science and technology, where efficiency meets innovation. As industries seek to maximize productivity and minimize costs, understanding the advanced techniques of starch drying becomes crucial.
The Role of High-Efficiency Dryers in Starch Processing
Flash dryers and fluidized bed dryers are at the forefront of starch drying technology. Flash dryers, for instance, utilize high-speed hot air flow to evaporate moisture quickly and efficiently, making them ideal for heat-sensitive starches. This method is not only rapid but also reduces the risk of thermal degradation, preserving the starch’s inherent qualities.
Fluidized bed dryers offer another layer of efficiency by enhancing the contact between starch granules and the drying air. This method promotes uniform drying, essential for maintaining consistent quality across batches. The gentle drying action helps prevent the physical damage often associated with other drying techniques, ensuring the production of high-quality dry starch suitable for various applications.
Customization and Control: Key Factors in Modern Starch Drying
The ability to control processing parameters precisely is what sets modern drying technologies apart. Automatic control systems in starch drying equipment allow for meticulous adjustment of temperature, humidity, and drying time. This level of control is critical for adapting the drying process to the specific needs of different types of starch, each with unique moisture content and thermal properties.
Moreover, today’s dryers are designed with energy efficiency in mind. Advanced heat recovery systems and optimized airflow patterns reduce energy consumption, aligning with the global push towards sustainable industrial practices.
Addressing the Challenges of Scale and Application
Adapting these technologies to handle different scales of operation—from small specialty batches in bespoke food systems to large-scale industrial production—is a testament to the versatility of modern starch drying solutions. Each facility must consider its capacity, from modest 2-ton daily operations to massive 300-ton outputs, ensuring that the technology can scale appropriately without compromising efficiency or product quality.
This scalability is complemented by a versatility that allows starch drying technologies to be tailored for various raw materials, such as corn, cassava, and potato starches. Each material brings its own set of challenges and benefits to the drying process, requiring customized solutions that cater to specific industrial needs.
By integrating these advanced technologies, industries can achieve superior drying outcomes, ensuring that the starch not only meets the stringent quality standards required for food products and industrial applications but also exhibits enhanced functional properties that are critical for end-use applications.

Elevate Your Industrial Capabilities with ICARUS Starch Drying Solutions
At ICARUS, we understand the critical importance of starch drying in maximizing product quality and operational efficiency. Our state-of-the-art finned tube heat exchangers are specifically designed to enhance the starch drying process, ensuring optimal thermal efficiency and superior drying performance.
Tailored Solutions for Every Need
Whether you are operating a small-scale cassava starch processing plant or a large-scale corn starch production line, ICARUS offers customized solutions that fit your specific requirements. Our equipment is engineered to handle a wide range of production capacities, from 2 tons to 300 tons per day, with the precision and reliability our clients have come to expect.
A Partnership for Innovation
Choosing ICARUS means more than just acquiring advanced technology; it means partnering with a leader in heat exchange solutions. We pride ourselves on our collaborative approach, working closely with our clients to understand their unique challenges and providing tailored solutions that not only meet but exceed their expectations.
Invitation to Discover Excellence
We invite you to explore the benefits of our finned tube heat exchangers and discover how ICARUS can transform your starch drying process. Whether you are looking to enhance efficiency, reduce energy consumption, or improve product quality, our team is ready to assist you with top-tier equipment and expert advice. Connect with us today to learn more about our solutions and how we can help elevate your production to the next level.
Request a quotation
Elevate your efficiency with Dutch-engineered solutions tailored for your needs. Fill out the details below, and our team will provide a personalized quote to help you harness the power of optimized energy in manufacturing. Step into the future, one quote at a time.
ICARUS Heat Exchangers