ADVANCING INDUSTRIAL EFFICIENCY AND SUSTAINABILITY
AIR COOLED HEAT EXCHANGER
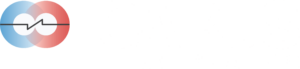
Elevating global standards with exceptional, unmatched Dutch craftsmanship in advanced industrial heat exchange.
Introduction to air cooled heat exchangers
Understanding the Mechanics: How They Work
Air cooled heat exchangers, an essential component in modern industrial processes, stand out as a sustainable solution in thermal transfer technology. These exchangers utilize ambient air to dissipate heat, negating the need for water like a condenser, thereby conserving this precious resource. Their adaptability across various industries, including chemical plants, power stations, and oil coolers, makes them invaluable.
At the core of air cooled heat exchangers lies the principle of convective thermal energy transfer. Hot process fluid flows through finned tubes, while fans mounted on the units draw ambient air across these tubes. This air absorbs the heat, effectively cooling the fluid. The design ensures an optimal air-side heat transfer coefficient, enhancing the unit’s efficiency. This will bring several benefits.
- Water Conservation: A great advantage, especially in areas with water scarcity.
- Reduced Maintenance: With fewer moving parts and no need for water treatment facilities, these exchangers are low-maintenance.
- Versatility and Adaptability: They can be used in a wide range of temperatures and pressures.
- Environmentally Friendly: Minimizes water usage and chemical treatment, reducing environmental impact.


Dutch excellence in heat exchange
At ICARUS Heat Exchangers, we blend Dutch craftsmanship with innovative technology, redefining the gold standard for industrial heat exchangers. Dive into the future of sustainable manufacturing, where our Dutch-engineered solutions elevate energy efficiency to unparalleled heights.
Lower total cost of ownership (TCO)
We go beyond performance with our heat exchangers, sculpting an unbeatable blend of.
Direct manufacturer benefits
Your unique needs are our command. We offer tailored heat exchanger solutions.
Customized solutions
With ICARUS Industrial, you're not just buying a product, you're engaging a partnership. Our direct sales model
Superior durability
Built from robust materials, our heat exchangers are a testament to resilience. They reduce maintenance
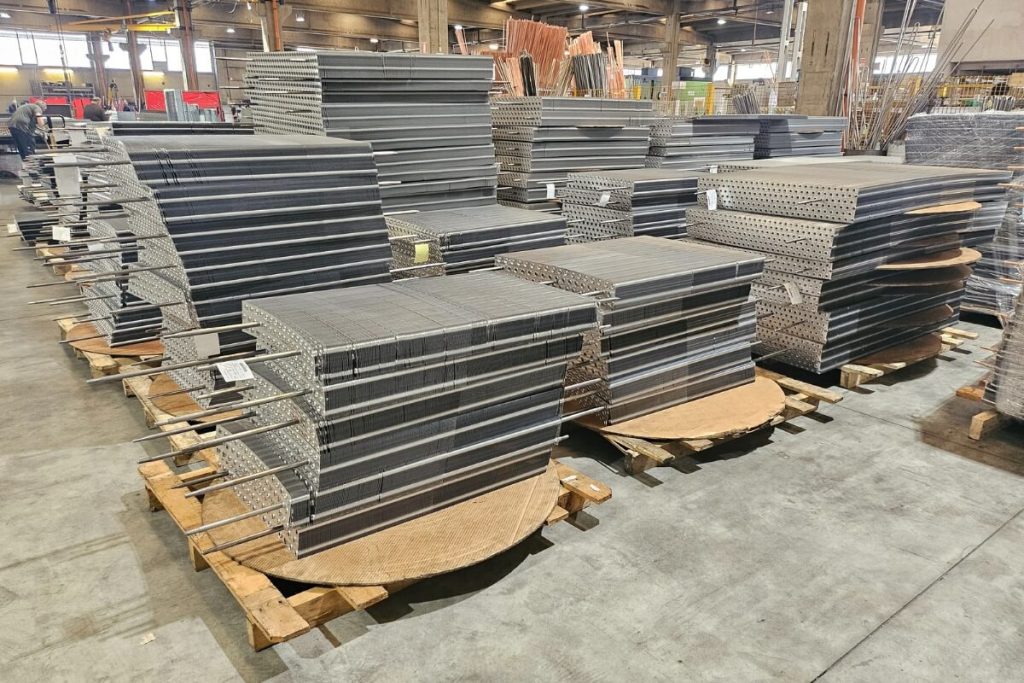
A Step Ahead in Innovation
At ICARUS Heat Exchangers, we specialize in industrial and electrical thermal energy exchangers. Our products are a testament to excellence in heating and cooling technology. We pride ourselves on our innovative and sustainable solutions, ensuring energy efficiency and reduced maintenance costs for our clients.
Advancements and Applications
The domain of air-cooled heat exchangers is witnessing rapid advancements, propelling its applications to new heights. Innovations such as improved finned tube types and advanced fan designs are revolutionizing the heat exchanger design, significantly enhancing thermal performance. These developments are crucial in optimizing the heat transfer surface and reducing the pressure drop, which in turn increases efficiency under various operating conditions.
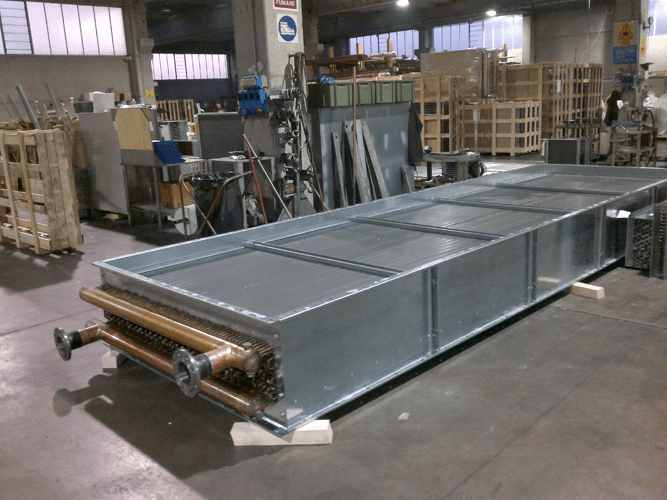
ICARUS's Unique Approach
Our approach at ICARUS involves integrating these advancements with our bespoke engineering. We focus on performance upgrades and reliability, ensuring that our heat exchangers not only meet but exceed industry standards.
- Enhanced Air Flow Design: Maximizing the rate of air flow for superior cooling efficiency.
- Robust Material Selection: Utilizing materials like aluminum and stainless steel for durability.
- Customization: Tailoring solutions to specific industrial needs.


Handling diverse design pressures
These exchangers, now more adept at handling diverse design pressures, are increasingly being employed in a wide range of applications. From serving as process coolers in petrochemical plants to managing thermal loads in gas compression systems, their versatility is unmatched. The enhanced design temperature capabilities allow for efficient operation across different ambient and process temperatures, making them suitable for both high and low-temperature applications.
Integration of heat integration techniques
One of the key advancements in this field is the integration of heat integration techniques. This approach maximizes the efficiency of the heat exchanger by effectively utilizing the available thermal energy, thereby minimizing energy waste. In pressure applications, the robust design pressure handling of these exchangers ensures reliability and safety, even under extreme conditions.
Furthermore, the advancements in air-cooled heat exchangers have led to more effective direct cooling methods. The ability to use a single unit for cooling, with precise control over inlet temperatures, has simplified processes and reduced costs. The incorporation of features to prevent warm or hot air recirculation has further enhanced their efficiency, making sure that the systems are not just cooling but also maintaining the desired process temperatures efficiently.
Environmental Impact and Sustainability
Air cooled thermal energy exchangers play a significant role in promoting environmental sustainability. By reducing water usage and avoiding the release of harmful chemicals into water bodies, these units contribute positively to environmental conservation efforts.
ICARUS's Commitment to the Environment
Our commitment at ICARUS extends beyond product excellence. We are dedicated to environmental stewardship, ensuring that our thermal energy exchangers are not only efficient but also eco-friendly. We continually strive to innovate in ways that reduce the ecological footprint of our products.
Eco-Friendly Features:
- Low Water Usage: Significantly reduces the strain on water resources.
- Energy Efficiency: Optimized designs lead to lower energy consumption.
- Reduced Chemical Treatment: Minimizes the use of hazardous chemicals.
Air cooled heat exchangers are a cornerstone in industrial thermal management. They offer a blend of efficiency, sustainability, and adaptability. At ICARUS Heat Exchangers, we are proud to deliver solutions that are not just effective but also responsible. Join us in embracing a future where industrial efficiency harmonizes with environmental consciousness.

Download a sample DWG
Discover precision engineering: Download a sample DWG of our top-notch heat exchangers.


Industrial heat exchangers at ICARUS
Redefining Industrial Efficiency with us
In a world where industrial efficiency is paramount, our heat exchangers at the forefront of innovation and reliability. Our Dutch-engineered air cooled heat exchangers are not just products; they are part of our dedication to excellence and sustainability in thermal transfer technology. Experience a new era of enhanced energy efficiency and reduced maintenance in your industrial processes.
Why Choose ICARUS?
- Innovative Design: Our cutting-edge designs incorporate the latest advancements in air cooled heat exchanger technology, ensuring superior performance.
- Customized Solutions: We understand that each industry has unique needs. That’s why we offer bespoke solutions, tailor-made to fit your specific requirements.
- Sustainability at Core: Our commitment to the environment is unwavering. ICARUS products are designed to minimize ecological impact while maximizing efficiency.
- Reduced Operating Costs: With our focus on energy efficiency and low maintenance, ICARUS heat exchangers help you save on operating costs, making them a cost-effective choice for your business.
- Unparalleled Quality: Quality is not just a feature; it’s our promise. Our thermal energy exchangers are built to last, using only the best materials and the most robust construction techniques.
- Enhanced Thermal Efficiency: Optimize your processes with our high-performance thermal energy exchangers.
- Durable and Reliable: Built to withstand the toughest industrial conditions.
- Expert Support: Our team of experts is always ready to provide you with the support and advice you need, ensuring your ICARUS experience is seamless and satisfactory.
In choosing thermal energy exchangers, you’re not just selecting a product; you’re partnering with a leader in thermal technology. You’re choosing a path of innovation, efficiency, and sustainability. Let ICARUS be the catalyst in your journey towards a more efficient and environmentally conscious industrial process.
Request a quotation
Elevate your efficiency with Dutch-engineered solutions tailored for your needs. Fill out the details below, and our team will provide a personalized quote to help you harness the power of optimized energy in manufacturing. Step into the future, one quote at a time.
ICARUS Heat Exchangers
Quotation Form
Frequently Asked Questions About Air Cooled Heat Exchangers
What are Air Cooled Heat Exchangers and How Do They Work?
Air cooled heat exchangers use ambient air to cool or condense process fluids, eliminating the need for water. They consist of finned tubes through which the process fluid flows. Fans blow air over these tubes, dissipating thermal energy from the fluid.
What Makes ICARUS Heat Exchangers Stand Out?
Our Heat Exchangers are renowned for their Dutch-engineered quality, innovative design, and commitment to sustainability. Our exchangers offer enhanced energy efficiency, reduced maintenance costs, and are tailored to meet specific industrial requirements.
Are Air Cooled Heat Exchangers Environmentally Friendly?
Absolutely. They significantly reduce water usage and chemical treatment, making them a more sustainable option compared to water-cooled systems.
Can These Exchangers Be Used in Any Industry?
Yes, they are versatile and adaptable for various industries, including oil and gas, power generation, and chemical processing.
How Do Air Cooled Heat Exchangers Conserve Water?
By using air instead of water for cooling, these exchangers eliminate the need for large volumes of water, conserving this vital resource.
What Are the Maintenance Requirements for Air Cooled Heat Exchangers?
They generally require less maintenance than water-cooled systems. Regular cleaning of fan blades and finned tubes is usually sufficient.
Can ICARUS Heat Exchangers Be Customized?
Yes, we offer customized solutions tailored to meet specific process requirements and industry standards.
What Is the Lifespan of an ICARUS Air Cooled Heat Exchanger?
Thermal energy exchangers are designed for longevity. With proper maintenance, they can operate efficiently for many years.
How Do Heat Exchangers Enhance Energy Efficiency?
By optimizing design elements like finned tube types and fan efficiency, our exchangers maximize thermal energy transfer while minimizing energy consumption.
What Materials Are Used in your Heat Exchangers?
We primarily use durable materials like aluminum and stainless steel to ensure longevity and resistance to harsh industrial environments.
In conclusion, ICARUS Heat Exchangers not only stand for quality and efficiency but also embody our commitment to sustainability and innovation. Our solutions are tailored to meet the evolving needs of industries worldwide, ensuring that your investment in our technology is a step towards a more efficient and environmentally responsible future.